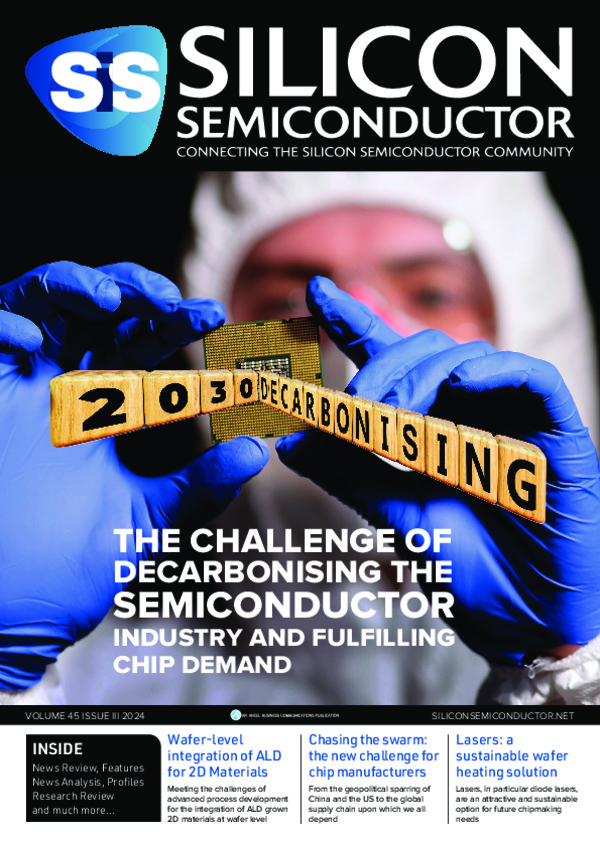
The challenge of decarbonizing the semiconductor industry and fulfilling chip demand
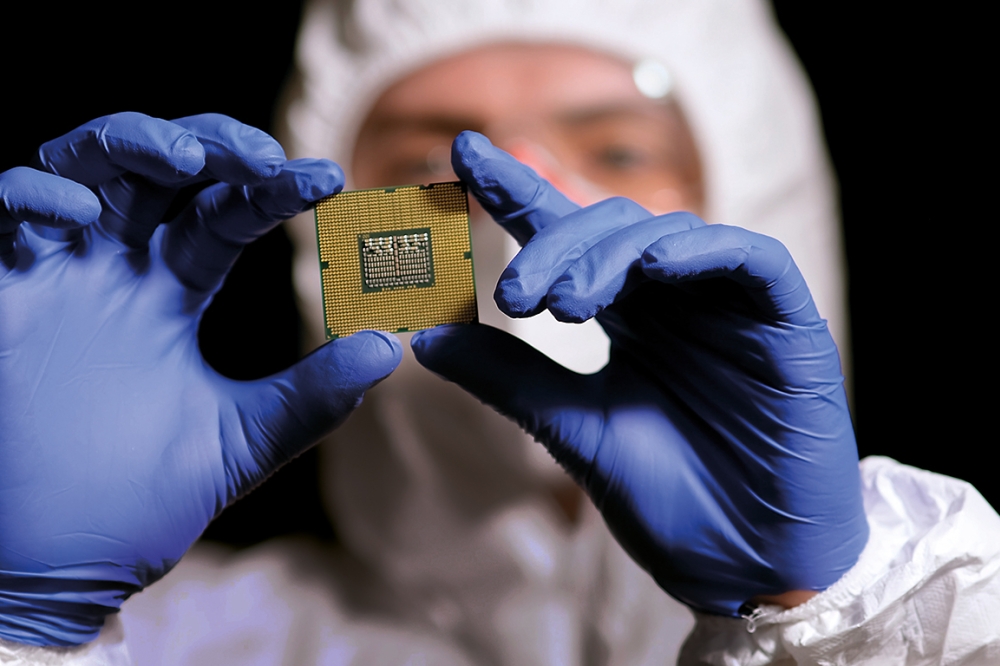
The semiconductor sector is an essential part of our increasingly digital environment. Its technologies, which include cell phones and computers we use for communication, the vehicles and aircraft that allow us to transport, the medical equipment that aids in disease diagnosis and treatment, and the grid systems that power our cities, are essential to everyday life. There can’t be a future without semiconductors, but their widespread use also presents growing environmental challenges.
By Henri Berthe, Semiconductor Vice President, Schneider Electric
The environmental cost of semiconductors
To meet demand, semiconductor players are building new fabrication plants (FABS), which can use as much as 100 megawatt-hours of power each hour—more than many automotive plants or oil refinery. This massive amount of electricity consumption will result in significant waste generation, greenhouse gas emissions and large carbon footprint In 2020, the industry emitted an astounding 41 million tonnes[VT2] of CO2, the equivalent of 5 million houses' annual emissions. And by 2030, semiconductor manufacturing is projected to consume 237 TWh of electricity globally, around equal to Australia's total 2021 electrical consumption.
As electronics grow in importance, manufacturers must navigate concerns around energy consumption and sustainability. Recent McKinsey research finds that major semiconductor companies’ latest commitments are still falling short of what is required under the 2016 Paris Agreement. As a result, businesses that fail to make their operations more environmentally friendly may face stronger restrictions and sanctions from future governments, as well as decreasing orders from increasingly environmentally sensitive customers. Conversely, those who optimise their energy efficiency early will unlock considerable resource savings and huge opportunities for growth.To protect their businesses’ futures, it is essential for manufacturers to start establishing sustainable practices today.
Upholding sustainability with resilience
Aside from environmental problems, many manufacturers are still dealing with the fallout from the global semiconductor crisis. A ‘perfect storm’ of global events almost brought production to a standstill throughout the pandemic: COVID-19's lockdowns both accelerated demand for consumer electronics and closed the factories producing the required components. Meanwhile, the China–United States trade war, Russia–Ukraine war, severe weather events, production facility fires, and a general reliance on semiconductor imports, rather than domestic manufacturing, also contributed to the sustained scarcity.
At the height of the chip shortage, research indicated that up to 169 businesses were affected globally. The consumer electronics and automotive industries took the brunt of the damage. PlayStation 5 consoles became akin to gold dust and Apple slashed its iPhone manufacturing targets, while Toyota reduced car manufacturing by 40% and General Motors paused vehicle production across North American plants.
Overall, the shortage cost the auto industry as much as $210 billion in revenue in 2021. And though manufacturers have now adapted to a constrained supply, increasingly complex products, such as electric vehicles with advanced safety and autonomy systems, will continue to accelerate semiconductor demand and spark a significant change in the manufacturing landscape.
As semiconductor production has been concentrated in Asia for the past 10 years, organisations and countries are now looking to create more diverse, resilient supply chains. In October 2022, the US government administered export control rules to constrain China’s production of the world’s most advanced chips. Meanwhile, the EU also intends to become a significant player through the European Chips Act. As investments shift from APAC to North America and Europe, manufacturers must be ready to offer low-carbon services to stand out from their competitors.
The three-step plan for resilience and sustainability
Determining an environmental baseline is a ‘must’ when decarbonizing the chip industry. At Schneider Electric, we’ve identified three key steps that help semiconductor organizations of all types and sizes to turn sustainable, net-zero ambitions into action.
The first step, called ‘Strategize’, involves measuring a manufacturer’s current energy performance and carbon footprint, and then crafting a net-zero plan that delivers tangible results. In reality, this involves establishing a baseline for carbon emissions, examining digital technologies to identify gaps and inform future roadmaps, assessing technical and economic feasibility to prioritize actions, and modelling building retrofit scenarios to develop a roadmap and timeline. The use of electrical digital twins when designing and simulating new FABS power systems in particular will improve their designs and optimise the network to meet local requirements and standards.
The second step is ‘Digitize’. This means creating a digital hub that can monitor and visualize a semiconductor organization's energy and resource usage, enabling leaders to make data-driven sustainability decisions and report on progress towards set goals. This single source of truth aids in the tracking of embedded carbon, including building information modelling, as well as the measurement of energy and carbon, including centralizing energy supply and utility data and implementing cloud-based, AI-powered analysis.
Finally, the third step is ‘Decarbonize’. This is where the true action takes place, in which semiconductor manufacturers must leverage insights from their Strategize and Decarbonize steps to make genuine sustainability improvements. Exact upgrades will depend on their findings, but examples include the electrification of fleet vehicles, the installation of renewable energy generators, the purchase of low or no-carbon products, and the use of AI to optimize on-site energy consumption in real-time.
Collaborating with dependable advisors and specialised partners
Alongside the three-step Strategize, Digitize, Decarbonize process, collaboration and partnerships are pivotal to achieving sustainability success in the semiconductor industry. With long-term sustainability requiring disparate areas of specialization and support, manufacturers must realize that no single company can accomplish it alone. Instead, semiconductor producers and vendors must work together and leverage external expertise and technology.
Schneider Electric has long been instrumental in assisting semiconductor companies in addressing sustainability and decarbonization challenges. For example, it recently partnered with Intel, one of the world’s leading semiconductor design and manufacturing companies, and Applied Materials, Inc., the world’s largest semiconductor and display equipment company, to launch Catalyze: a new partnership program aimed at accelerating access to renewable energy across the global semiconductor value chain.
With the assistance of the Catalyze program, semiconductor leaders will be able to achieve a number of sustainability and resilience goals, including:
• Combine energy purchasing power across the semiconductor value chain to accelerate the deployment of renewable energy projects
• Participate in the market for utility-scale power purchase agreements (PPAs)
• Develop operational models to be used in supply chain programs to close net-zero ambition gaps
• Increase awareness of the availability of renewable energy in specific global regions where the semiconductor value chain is operational
• Lead the way for the industry to drive definitive next steps
Sustainable power in the manufacturing of semiconductors
Ultimately, embracing sustainability measures not only aligns with global environmental goals, but also makes sense for semiconductor fabrication plants’ bottom lines. Studies indicate that implementing sustainability strategies can reduce costs and positively impact operating profit by up to 60%. Moreover, adopting sustainability practices mitigates long-term risks and opens opportunities in new markets.
Now that we’ve seemingly progressed from the semiconductor crisis , manufacturers have potential for enormous growth through long-term improvements. They can produce large savings as well as unlock enormous untouched energy efficiency possibilities. And the best part? The tools to achieve this are right in front of us. With the help of a knowledgeable network of partners, organisations must learn to decarbonize, digitize, and strategize today.